PRODUCT PARAMETERS
Description
Introduction of Rotary Kiln
A rotary kiln is a kind of industrial equipment used for material heating and processing, which is widely used in cement, metallurgy, chemical industry, etc. Rotary Kiln refers to various parts and components which are necessary for maintaining and repairing the normal operation of the rotary kiln, such as cylinder, baffle wheel, pallet, sealing device and so on.
Features and advantages of Rotary Kiln
High-temperature resistance: Due to the extremely high temperature of the working environment of the rotary kiln, the spare parts are usually made of refractory materials or special alloys to ensure that they can work stably under high temperatures.
High abrasion resistance: Long time material friction and chemical erosion require spare parts to have excellent abrasion resistance to prolong service life.
High structural strength: in order to withstand heavy loads and the pressure of continuous operation, the design of spare parts will place special emphasis on structural strength and reliability.
Easy to install and maintain: Considering the need for frequent replacement, many spare parts are designed to be simpler and easier for quick installation and maintenance.
Strong adaptability: different industries have different needs for rotary kilns, so spare parts need to have good versatility and adaptability to meet diverse application conditions.
(Rotary Kiln)
Specifications of Rotary Kiln
A rotating kiln is a high-temperature handling devices utilized in various industries such as concrete, lime, metallurgy, and chemical processing. Below are the key specifications generally related to rotating kilns:
** Style & Capacities **: Rotating kilns are cylindrical vessels with sizes ranging from 1.5 meters to over 5 meters and sizes prolonging from 15 meters to 230 meters, depending on the application. The kiln is slightly inclined (1-4 degrees) to facilitate material activity.
** Rotation Speed **: Adjustable rotation speeds, normally between 0.5 to 5 RPM, regulate the residence time of products inside the kiln. Variable-frequency drives allow precise rate guideline.
** Operating Temperature Level **: Developed to stand up to severe temperature levels, rotating kilns operate between 800 ° C to 1,800 ° C, depending on the procedure. Refractory cellular linings secure the steel covering from warm and deterioration.
** Product Throughput **: Capacity differs by dimension and application, ranging from 500 tons/day for tiny kilns to over 12,000 tons/day for large-scale cement production.
** Gas Type **: Compatible with multiple fuels, including gas, coal, oil, biomass, or alternate fuels. Heaters are developed for effective combustion and temperature level harmony.
** Drive System **: Powered by electric motors (50-1,000 kW) combined with transmissions and girth equipments. Supporting drives make certain rotation throughout power failures or maintenance.
** Refractory Lining **: High-alumina, magnesite, or fireclay blocks line the inside, with densities from 150 mm to 300 mm, customized to thermal and chemical needs.
** Air Conditioning & Warmth Recuperation **: Optional air conditioning systems, such as air-quenching or water jackets, manage outside temperature levels. Warmth exchangers recoup waste warm for power performance.
** Emissions Control **: Integrated with dust collection agencies, scrubbers, or electrostatic precipitators to decrease particulate matter, NOx, and SOx discharges, complying with environmental criteria.
** Instrumentation & Automation **: Furnished with thermocouples, pressure sensing units, and gas analyzers for real-time tracking. PLC-based systems automate temperature, air movement, and product feed.
** Applications **: Used for calcination, sintering, decrease, and thermal treatment of products like limestone, cement clinker, iron ore, and waste products.
** Personalization **: Kilns are tailored to customer needs, including material-specific linings, specialized seals, preheaters, or afterburners.
Rotary kilns are crafted for longevity, efficiency, and scalability, making certain optimum efficiency in demanding industrial environments.
(Rotary Kiln)
Applications of Rotary Kiln
Rotary kilns are functional thermal handling systems used throughout numerous industries to promote high-temperature chemical reactions and product changes. Their round style, rotational movement, and controlled heating make them optimal for continuous handling of bulk materials. Below are vital applications of rotating kilns.
In the concrete sector, rotary kilns are main to clinker manufacturing. Resources like limestone, clay, and iron ore are fed right into the kiln and heated to around 1450 ° C, triggering calcination and chemical bonding to create clinker, which is later ground into concrete.
Lime production relies on rotating kilns to calcine sedimentary rock (calcium carbonate) right into quicklime (calcium oxide) at temperature levels going beyond 900 ° C. This procedure is crucial for steelmaking, water therapy, and construction.
Metallurgical applications consist of processing ores and focuses. Rotary kilns roast, lower, or scented steels like iron, light weight aluminum, and zinc. For example, they convert iron ore right into pellets for blast heating systems or improve bauxite into alumina for aluminum manufacturing.
In waste management, rotating kilns serve as burners for dangerous and medical waste. They safely disintegrate toxic materials at heats (1200– 1400 ° C), guaranteeing regulatory compliance and lowering ecological influence. They additionally refine local strong waste right into inert ash or recover power through waste-to-energy systems.
The chemical industry utilizes rotating kilns to produce catalysts, pigments, and specialty chemicals. For example, titanium dioxide (a common pigment) is manufactured by calcining titanium slag in rotary kilns. They additionally restore invested drivers by removing contaminations.
Mineral processing applications consist of refining kaolin, plaster, and phosphate. Kilns enhance material homes through calcination, enhancing illumination, solubility, or sensitivity for usage in ceramics, fertilizers, and construction products.
Ecological remediation tasks use rotating kilns to treat polluted dirt by thermally destroying toxins like hydrocarbons or hefty steels.
Rotary kilns are also made use of in carbonization (e.g., transforming biomass to biochar) and oil coke calcining. Their flexibility to diverse materials, power effectiveness, and scalability make them vital in hefty sectors. Developments in refractory products, warmth healing, and automation even more boost their performance, sustainability, and cost-effectiveness, solidifying their duty in contemporary production and ecological remedies.
Company Introduction
Established in 2001, plant Machinery Equipment Co.,ltd. focus on metal research and mining machinery spare parts. 2 factories over an area of 13,300 square meters, based on 100+ sets of equipment, our production capacity reaches 12000 Tons/Year. has passed ISO 9001 quality managment system certification in 2008.
Our mainly products are dragline excavator spare parts,rotary kiln spare parts, large modulus gear (gear shaft), gearbox ect. 40+ patents with over 45 years experience to help focus on improve the service life of spare parts. We belive that more than 80% reason of mechanical parts’ working life depends on hot processing (steel making/forging/casting/welding/heat treatment). Eight material engineers will control the quality from the original resource.
If you are interested, please feel free to contact us.
Payment
L/C, T/T, Western Union, Paypal, Credit Card etc.
Shipment
By sea, by air, by express, as customers request.
5 FAQs of Rotary Kiln
What is a rotary kiln? A rotary kiln is a large, cylindrical thermal processing furnace used to heat raw materials at high temperatures to induce chemical or physical changes. It is commonly employed in industries like cement production, lime manufacturing, and metallurgy. The kiln rotates slowly to ensure even heat distribution and efficient material processing, converting inputs like limestone, iron ore, or waste materials into finished products through calcination, reduction, or pyrolysis.
Which industries use rotary kilns? Rotary kilns are versatile and used across multiple industries. The cement industry relies on them for clinker production, while the lime industry uses kilns to calcine limestone. Chemical plants employ rotary kilns for catalyst regeneration or titanium dioxide production. They’re also used in waste management for hazardous material treatment and in metallurgy for ore refining. Environmental applications include soil remediation and biomass processing.
How does a rotary kiln work? The kiln is a slightly inclined rotating cylinder. Raw materials are fed into the upper end, and as the kiln rotates, gravity moves them toward the lower end. Burners at the lower end generate heat (up to 1,450°C), creating distinct temperature zones. Materials undergo drying, calcination, and sintering as they travel through these zones, exiting as processed product.
What are the key components of a rotary kiln? The main components include the rotating shell (lined with refractory material), drive system (gears, motors), support rollers and bearings, seals to prevent heat loss, and burners for fuel combustion. Auxiliary systems include feed and discharge mechanisms, exhaust gas handling, and temperature control instruments.
How to maintain a rotary kiln? Regular maintenance is critical. Inspect refractory linings for wear and replace damaged sections. Monitor support rollers and bearings for alignment and lubrication. Check drive systems for smooth operation. Track temperature profiles to avoid overheating. Clean heat exchangers and ducts to prevent blockages. Schedule downtime for preventive checks to minimize unplanned outages and extend equipment lifespan.
What factors determine rotary kiln selection? Key factors include material type (moisture, granulometry), required processing temperature, residence time, energy efficiency goals, and emission regulations. Kiln size, rotational speed, inclination angle, and burner capacity are tailored to these needs. Consider operational costs, maintenance requirements, and compliance with environmental standards when choosing a design.
(Rotary Kiln)
REQUEST A QUOTE
RELATED PRODUCTS
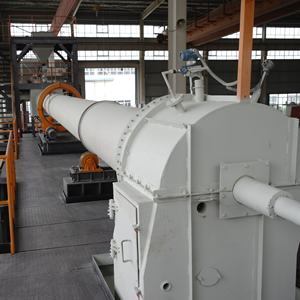
HZG RDF / Municipal Waste / Electroplating Sludge Rotary Kiln Dryer
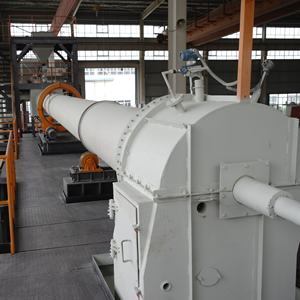
OEM Steel Rotary Kiln Support Roller Shaft
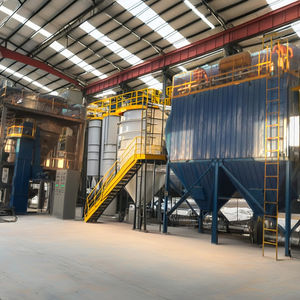
Rotary kiln and cement ball mill spare pasts wheel and ring gear casting girth gear large steel spur gear
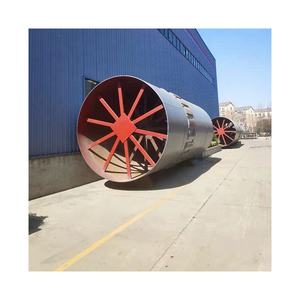
220V 380V 230V High Temperature Resistance Plastic Machine Ceramic Heater Element
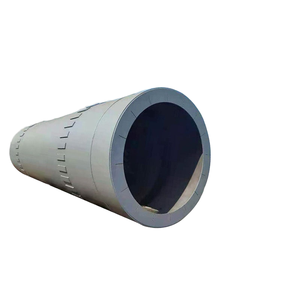
New-tech high quality pyrolysis rotary kiln ore roasting rotary kiln
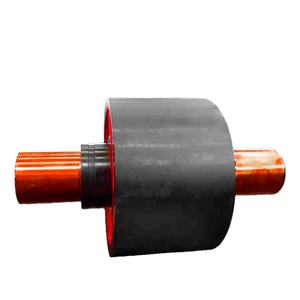