PRODUCT PARAMETERS
Description
Introduction of Metallurgy Rotary Kiln for Iron Ore Pellets Roasting/Sponge Iron Ore Magnetizing Roast Rotary Kiln
A rotary kiln is a kind of industrial equipment used for material heating and processing, which is widely used in cement, metallurgy, chemical industry, etc. Metallurgy Rotary Kiln for Iron Ore Pellets Roasting/Sponge Iron Ore Magnetizing Roast Rotary Kiln refers to various parts and components which are necessary for maintaining and repairing the normal operation of the rotary kiln, such as cylinder, baffle wheel, pallet, sealing device and so on.
Features and advantages of Metallurgy Rotary Kiln for Iron Ore Pellets Roasting/Sponge Iron Ore Magnetizing Roast Rotary Kiln
High-temperature resistance: Due to the extremely high temperature of the working environment of the rotary kiln, the spare parts are usually made of refractory materials or special alloys to ensure that they can work stably under high temperatures.
High abrasion resistance: Long time material friction and chemical erosion require spare parts to have excellent abrasion resistance to prolong service life.
High structural strength: in order to withstand heavy loads and the pressure of continuous operation, the design of spare parts will place special emphasis on structural strength and reliability.
Easy to install and maintain: Considering the need for frequent replacement, many spare parts are designed to be simpler and easier for quick installation and maintenance.
Strong adaptability: different industries have different needs for rotary kilns, so spare parts need to have good versatility and adaptability to meet diverse application conditions.
(Metallurgy Rotary Kiln for Iron Ore Pellets Roasting/Sponge Iron Ore Magnetizing Roast Rotary Kiln)
Specifications of Metallurgy Rotary Kiln for Iron Ore Pellets Roasting/Sponge Iron Ore Magnetizing Roast Rotary Kiln
The metallurgy rotary kiln for iron ore pellets roasting handles high-temperature processing of iron ore pellets. It converts raw pellets right into set, usable kinds. The sponge iron ore alluring roast rotary kiln readjusts magnetic buildings of iron ore. It improves separation effectiveness in downstream processes. The kiln structure consists of a cylindrical steel covering. The shell is lined with refractory products. These products resist extreme heat. The kiln runs at temperature levels in between 900 ° C and 1300 ° C. This variety matches various ore types. The kiln rotates slowly. Turning ensures even heat distribution. It stops product clumping. The size ranges from 2.5 meters to 5 meters. Size differs from 30 meters to 75 meters. Size depends upon production needs. The kiln utilizes gas like coal, gas, or oil. Burners are placed at the kiln’s discharge end. Warmth streams towards the feed end. This counter-current design makes the most of energy effectiveness. The kiln’s incline angle is adjustable. Changes manage worldly activity rate. Processing time is enhanced. Airflow systems supply oxygen. They keep combustion security. Dirt collectors minimize exhausts. They meet ecological requirements. The drive system makes use of equipments and electric motors. It makes certain smooth rotation. Assistance rollers stabilize the kiln’s weight. They minimize mechanical wear. Temperature level sensors keep track of home heating areas. Information is sent out to a control board. Operators adjust parameters in actual time. Automated systems decrease human error. The cooling system decreases pellet temperature level after processing. Water or air cools down the outcome. This protects against re-oxidation. The kiln deals with alluring roast for sponge iron. It transforms hematite to magnetite. Magnetic splitting up ends up being less complicated. The kiln benefits both hematite and limonite ores. Maintenance includes regular checks of refractory cellular linings. Used sections are changed without delay. Lubrication of gears and rollers is regular. The kiln’s design lessens downtime. It increases manufacturing rates. Energy-saving features reduced functional expenses. Personalized configurations are readily available. They match particular ore qualities or outcome targets. The kiln is used in steel plants and mining procedures. It supports large commercial processes.
(Metallurgy Rotary Kiln for Iron Ore Pellets Roasting/Sponge Iron Ore Magnetizing Roast Rotary Kiln)
Applications of Metallurgy Rotary Kiln for Iron Ore Pellets Roasting/Sponge Iron Ore Magnetizing Roast Rotary Kiln
Metallurgy rotary kilns play a key role in processing iron ore pellets and sponge iron. These kilns warmth materials to heats to trigger chemical modifications. In iron ore pellet roasting, the rotating kiln transforms raw pellets into solidified, durable kinds. The process eliminates dampness and unstable contaminations. It additionally oxidizes the pellets to increase toughness for blast heating system use. The even heat distribution inside the kiln makes sure uniform top quality across batches. This reduces waste and enhances efficiency in steel manufacturing.
For sponge iron alluring roast, the rotating kiln adjusts iron ore’s magnetic residential or commercial properties. It transforms non-magnetic hematite into magnetic magnetite. This makes ore much easier to divide throughout beneficiation. The kiln operates under controlled temperatures and environments. Exact modifications let it deal with differing ore qualities. This versatility supports consistent outcome regardless of basic material distinctions.
These rotary kilns are constructed for heavy-duty efficiency. Their rotating layout prevents material clumping. This makes sure steady activity and exposure to warmth. Refractory cellular linings withstand severe temperature levels. Advanced sealing systems minimize heat loss. This cuts energy prices and expands equipment life. Automated controls keep track of temperature, air movement, and rotation speed. Operators can make improvements settings in genuine time for ideal outcomes.
Resilience is a significant benefit. Top notch products resist wear from abrasive ores. Reduced upkeep requires minimize downtime. The kilns adapt to numerous fuel kinds, consisting of coal, gas, or biomass. This makes them appropriate for diverse commercial setups. Their portable layout conserves area while delivering high output.
Industries rely upon these kilns for trusted, massive handling. They satisfy rigorous environmental criteria by decreasing exhausts. Reliable burning systems reduced carbon impacts. The innovation sustains lasting steelmaking practices. By boosting ore functionality, rotary kilns contribute to cost-effective steel production. Their duty in modern metallurgy remains crucial for both quality and productivity.
Company Introduction
Established in 2001, plant Machinery Equipment Co.,ltd. focus on metal research and mining machinery spare parts. 2 factories over an area of 13,300 square meters, based on 100+ sets of equipment, our production capacity reaches 12000 Tons/Year. has passed ISO 9001 quality managment system certification in 2008.
Our mainly products are dragline excavator spare parts,rotary kiln spare parts, large modulus gear (gear shaft), gearbox ect. 40+ patents with over 45 years experience to help focus on improve the service life of spare parts. We belive that more than 80% reason of mechanical parts’ working life depends on hot processing (steel making/forging/casting/welding/heat treatment). Eight material engineers will control the quality from the original resource.
If you are interested, please feel free to contact us.
Payment
L/C, T/T, Western Union, Paypal, Credit Card etc.
Shipment
By sea, by air, by express, as customers request.
5 FAQs of Metallurgy Rotary Kiln for Iron Ore Pellets Roasting/Sponge Iron Ore Magnetizing Roast Rotary Kiln
1. What does a rotary kiln do in iron ore processing?
A rotary kiln heats iron ore pellets or fines to specific temperatures. This changes their physical and chemical properties. The process removes moisture, volatiles, and impurities. It also oxidizes or reduces the ore depending on the goal. The result is roasted pellets or magnetized sponge iron ready for steelmaking.
2. What temperature range does the kiln use?
Temperatures vary based on the material and desired outcome. Iron ore pellets typically roast between 1200°C and 1300°C. Magnetizing roast for sponge iron requires lower temps, around 800°C to 1050°C. Precise control ensures consistent product quality. Heat comes from burners using fuels like coal, gas, or oil.
3. How long does the material stay inside the kiln?
Residence time depends on the kiln’s rotation speed, angle, and length. For pellets, it usually takes 10 to 40 minutes. Sponge iron processes might need longer times for reduction. Adjustments optimize efficiency and output. Sensors monitor progress to avoid under- or over-processing.
4. What maintenance does the kiln need?
Regular checks prevent breakdowns. Inspect refractory lining for wear and tear. Clean heat exchangers and seals to avoid leaks. Lubricate gears and bearings to reduce friction. Monitor burner nozzles for blockages. Scheduled downtime ensures long-term reliability.
5. Why choose this rotary kiln over others?
The design ensures even heat distribution and high thermal efficiency. It handles abrasive materials with minimal wear. Automation allows precise control of temperature and airflow. Energy recovery systems cut fuel costs. This setup suits large-scale production with low operating costs.
(Metallurgy Rotary Kiln for Iron Ore Pellets Roasting/Sponge Iron Ore Magnetizing Roast Rotary Kiln)
REQUEST A QUOTE
RELATED PRODUCTS
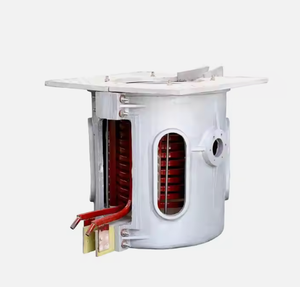
OEM rotary kiln girth gear alignment and Pinion Assembly For Rotary Kilns And Coolers
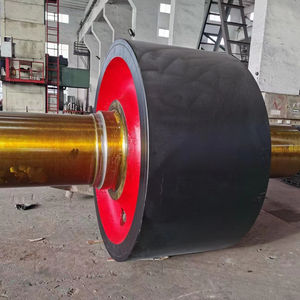
Environmental Protection Long Service Life Double Swirl Rotary Kiln Burner Advanced Double Swirl Rotary Kiln Burner
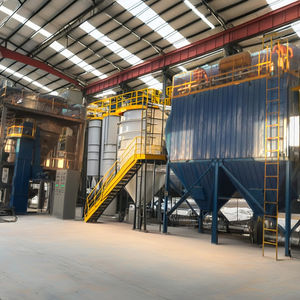
kiln chain steel round link welded rotary kiln chain stainless steel welded kiln chain
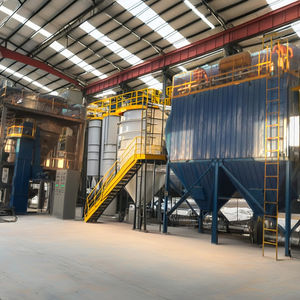
Laboratory Kiln 1100 1200 1400 1500 1600 1700 1800 Celsius Degree Electric Ceramic Box Melting Oven Vacuum Muffle Furnace
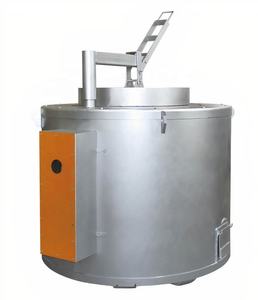
Four Channel Cement Rotary Kiln Industry Double Swirl Rotary Kiln Burner Double Swirl Rotary Kiln Burner For Cement Production
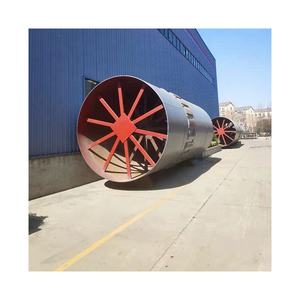