PRODUCT PARAMETERS
Description
Introduction to Rotary Drum Dryer For Quartz iron powder high temperature deimpurity calcination equipment
Rotary Drum Dryer For Quartz iron powder high temperature deimpurity calcination equipment is for repairing, replacing or upgrading worn, damaged or deteriorated parts in drying equipment. These spare parts can include heating elements, drums, belts, fans, temperature and humidity controls, etc., to ensure that the dryer will run efficiently and consistently.
Advantages and features of Rotary Drum Dryer For Quartz iron powder high temperature deimpurity calcination equipment
High-quality materials: manufactured using durable and heat-resistant materials to ensure long life and high reliability.
Precise Fit: Precisely designed for specific models of dryers to ensure easy installation and perfect fit.
Rapid Response: Provide fast spare parts supply service to reduce downtime and improve production efficiency.
Technical Support: Equipped with a professional technical support team to provide installation guidance and troubleshooting assistance.
Cost-effectiveness: Reduce long-term operating costs by extending the service life of the equipment.
(Rotary Drum Dryer For Quartz iron powder high temperature deimpurity calcination equipment)
Specifications of Rotary Drum Dryer For Quartz iron powder high temperature deimpurity calcination equipment
The Rotary Drum Dryer is built for high-temperature calcination of quartz iron powder. It removes impurities efficiently. The equipment operates within 800°C to 1200°C. This temperature range ensures effective purification. The drum measures 2.5 meters in diameter. It spans 12 meters in length. The large size supports continuous processing of bulk materials. The drum is constructed from heat-resistant stainless steel. It endures extreme temperatures over long periods. The system supports gas, electric, or coal heating. Users select the method based on cost and fuel availability. Power consumption is optimized for energy efficiency. Performance remains consistent despite lower energy use. Safety mechanisms include pressure relief valves. Temperature sensors track heat levels in real time. The control panel allows easy adjustment of settings. Operators set temperature, rotation speed, and processing time directly. Insulation layers reduce heat loss. The drum resists thermal stress. This extends its service life. Applications cover metallurgy, ceramics, and chemical industries. The dryer processes large material volumes smoothly. Custom drum sizes are available. Heating methods can be tailored to specific needs. Maintenance is straightforward. Access points enable quick inspections and part replacements. The equipment adheres to international industry standards. It performs reliably under demanding conditions. Production capacity reaches 15 tons per hour. The rotation speed adjusts between 3 to 8 RPM. Airflow systems ensure even heat distribution. Moisture content in materials drops below 0.5% after processing. Wear-resistant liners protect the drum interior. The drive system uses heavy-duty gears. Motor power ranges from 55 to 75 kW. Feed and discharge ports are automated. Dust collection units minimize environmental impact. The frame is reinforced for stability. Cooling systems prevent overheating. Technical support is available for installation and operation.
(Rotary Drum Dryer For Quartz iron powder high temperature deimpurity calcination equipment)
Applications of Rotary Drum Dryer For Quartz iron powder high temperature deimpurity calcination equipment
The rotary drum dryer serves as essential equipment in processing quartz and iron powder through high-temperature deimpurity calcination. Industries like metallurgy, construction, and chemical manufacturing rely on this machinery to purify raw materials. The process involves heating materials to extreme temperatures, effectively removing moisture, volatile substances, and impurities. This ensures the final product meets strict quality standards for industrial use.
The dryer’s cylindrical drum rotates steadily, exposing materials evenly to heat. Built from durable materials like stainless steel or refractory alloys, it withstands prolonged high-temperature operation. Heating methods vary, including gas, oil, or electric systems, tailored to specific production needs. The design maximizes heat transfer efficiency, reducing energy consumption while maintaining consistent output.
This equipment handles large volumes of quartz or iron powder continuously, streamlining production. Adjustable parameters like temperature, rotation speed, and processing time allow customization for different material grades. Automated controls monitor conditions in real time, minimizing human error. Safety features like pressure relief valves and thermal sensors prevent overheating or equipment damage.
In quartz processing, the dryer removes impurities like organic residues or metal oxides, enhancing purity for applications in glassmaking or ceramics. For iron powder, calcination eliminates sulfur, carbon, or other contaminants, improving quality for steel production. The system also processes minerals, chemicals, or recycled materials requiring thermal treatment.
High thermal efficiency lowers operational costs, making it cost-effective for large-scale projects. The closed design reduces dust emissions, aligning with environmental regulations. Heat recovery systems reuse excess energy, further cutting fuel expenses. Low maintenance requirements and easy access to components simplify upkeep, minimizing downtime.
Operators benefit from user-friendly interfaces, enabling quick adjustments without advanced technical skills. The robust construction ensures long-term reliability, even under harsh industrial conditions. By integrating advanced heating technology with precise control systems, the rotary drum dryer delivers consistent, high-quality results across diverse applications.
Company Introduction
Established in 2001, plant Machinery Equipment Co.,ltd. focus on metal research and mining machinery spare parts. 2 factories over an area of 13,300 square meters, based on 100+ sets of equipment, our production capacity reaches 12000 Tons/Year. has passed ISO 9001 quality managment system certification in 2008.
Our mainly products are dragline excavator spare parts,rotary kiln spare parts, large modulus gear (gear shaft), gearbox ect. 40+ patents with over 45 years experience to help focus on improve the service life of spare parts. We belive that more than 80% reason of mechanical parts’ working life depends on hot processing (steel making/forging/casting/welding/heat treatment). Eight material engineers will control the quality from the original resource.
If you are interested, please feel free to contact us.
Payment
L/C, T/T, Western Union, Paypal, Credit Card etc.
Shipment
By sea, by air, by express, as customers request.
5 FAQs of Rotary Drum Dryer For Quartz iron powder high temperature deimpurity calcination equipment
What is a rotary drum dryer used for in quartz iron powder processing? It removes moisture and impurities from quartz iron powder through high-temperature heating. The process involves rotating a heated drum to ensure even heat distribution. This method effectively dries the material while eliminating unwanted elements.
How does the high-temperature calcination process work? The dryer heats materials to temperatures between 800°C and 1200°C inside the rotating drum. The rotation mixes the powder for uniform exposure to heat. This breaks down impurities chemically. The result is purified quartz iron powder ready for industrial use.
What materials can this dryer handle? It processes quartz iron powder with varying moisture levels and impurity contents. The drum’s robust construction resists wear from abrasive materials. Adjustable temperature and rotation speed allow customization for different material grades. Consistent performance is maintained even with high workloads.
How is maintenance managed for this equipment? Regular inspection of heating elements and drum seals prevents breakdowns. Cleaning the drum interior avoids material buildup. Lubricating rotating parts ensures smooth operation. Replacing worn components like liners or bearings early reduces downtime. Proper maintenance extends the machine’s lifespan.
What safety features are included? The dryer has temperature sensors to prevent overheating. Emergency shutdown systems activate if abnormalities occur. Insulated exteriors protect operators from heat. Dust collection systems minimize airborne particles. Safety protocols are followed during operation to reduce risks. These features ensure safe handling of high-temperature processes.
(Rotary Drum Dryer For Quartz iron powder high temperature deimpurity calcination equipment)
REQUEST A QUOTE
RELATED PRODUCTS
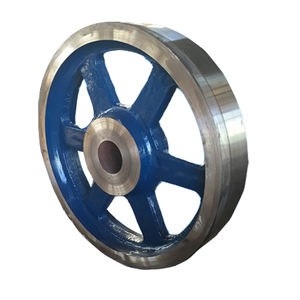
laundry 50kg new rotary drum match with washing machine dryer
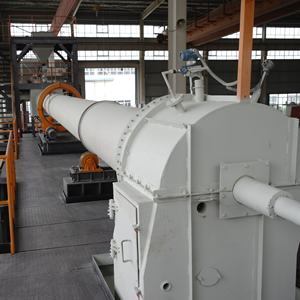
Wood Processing Made Easy: Rotary Drum Dryers for Timber
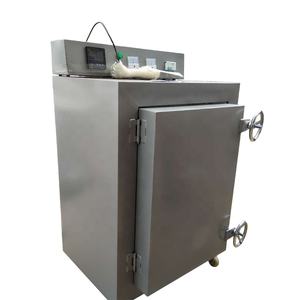
Factory Customized Drum Dryer Drying Rotary Drum Single Cylinder Dryers For Construction
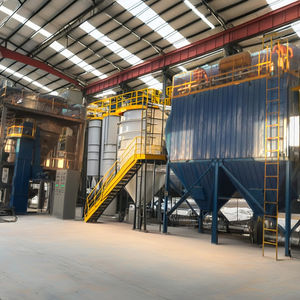
Eco-Friendly mini rotary drum dryer
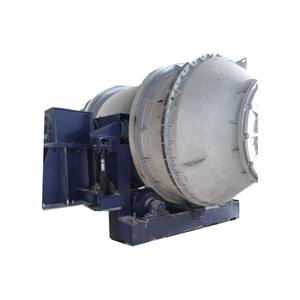
Best Rotary Drum Dryer for Coal Slime/Kaolin/Fertilizer/Lime/Slag/Sand
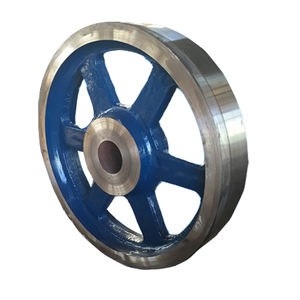