PRODUCT PARAMETERS
Description
Introduction of Direct Energy Saving Limestone Rotary Kiln Gypsum Production Line Rotary Kiln Coke Calcining Rotary Kiln
A rotary kiln is a kind of industrial equipment used for material heating and processing, which is widely used in cement, metallurgy, chemical industry, etc. Direct Energy Saving Limestone Rotary Kiln Gypsum Production Line Rotary Kiln Coke Calcining Rotary Kiln refers to various parts and components which are necessary for maintaining and repairing the normal operation of the rotary kiln, such as cylinder, baffle wheel, pallet, sealing device and so on.
Features and advantages of Direct Energy Saving Limestone Rotary Kiln Gypsum Production Line Rotary Kiln Coke Calcining Rotary Kiln
High-temperature resistance: Due to the extremely high temperature of the working environment of the rotary kiln, the spare parts are usually made of refractory materials or special alloys to ensure that they can work stably under high temperatures.
High abrasion resistance: Long time material friction and chemical erosion require spare parts to have excellent abrasion resistance to prolong service life.
High structural strength: in order to withstand heavy loads and the pressure of continuous operation, the design of spare parts will place special emphasis on structural strength and reliability.
Easy to install and maintain: Considering the need for frequent replacement, many spare parts are designed to be simpler and easier for quick installation and maintenance.
Strong adaptability: different industries have different needs for rotary kilns, so spare parts need to have good versatility and adaptability to meet diverse application conditions.
( Direct Energy Saving Limestone Rotary Kiln Gypsum Production Line Rotary Kiln Coke Calcining Rotary Kiln)
Specifications of Direct Energy Saving Limestone Rotary Kiln Gypsum Production Line Rotary Kiln Coke Calcining Rotary Kiln
This rotary kiln setup conserves energy directly in limestone processing. It uses a preheater and precalciner system. This style reduces gas use dramatically. The kiln manages limestone dimensions from 10mm to 50mm. Production capacity varies from 300 bunches to 5000 bunches daily. Running temperatures reach roughly 1350 ° C. This makes certain reliable calcination. The kiln shell turns steadily at 0.5 to 1.5 RPM. Refractory cellular linings hold up against high warm. This configuration generates high-grade quicklime accurately.
The gypsum production line rotating kiln transforms phosphogypsum or all-natural gypsum into stucco. It operates at reduced temperature levels. The range is typically 160 ° C to 180 ° C. This temperature de-waters the gypsum successfully. The kiln layout makes certain also home heating. Material house time within is very carefully controlled. This control guarantees consistent beta hemihydrate plaster powder. Manufacturing outcomes vary. They match various task ranges. The system is durable. It takes care of continuous operation well.
The coke calcining rotating kiln processes raw oil coke. Its function is eliminating unpredictable issue. It attains high pureness calcined coke. Running temperature levels are vital. They run between 1200 ° C and 1300 ° C. This warm repels volatiles successfully. The kiln features a certain length-to-diameter proportion. This proportion makes sure complete calcination. Cooling systems manage the hot coke discharge. The result is high-density, low-reactivity calcined coke. This coke is important for light weight aluminum smelting anodes. The kiln supplies high throughput. It meets requiring industrial requirements.
( Direct Energy Saving Limestone Rotary Kiln Gypsum Production Line Rotary Kiln Coke Calcining Rotary Kiln)
Applications of Direct Energy Saving Limestone Rotary Kiln Gypsum Production Line Rotary Kiln Coke Calcining Rotary Kiln
Direct energy conserving limestone rotary kilns deal with manufacturing costs head-on. These kilns recover warm properly. They make use of less gas during sedimentary rock handling. This reduces energy bills dramatically. Lower operating costs imply better revenues. The design prevents warm waste. It keeps temperatures consistent inside. This ensures trustworthy sedimentary rock calcination. Result high quality remains high consistently. Gas financial savings are genuine and quantifiable.
Plaster assembly line rotary kilns handle dehydration efficiently. They transform gypsum rock into powder. The process requires specific temperature control. These kilns provide that control accurately. They keep also warm circulation. This protects against material over-burning or under-cooking. Consistent gypsum powder high quality results. Production lines run much longer without quiting. Upkeep requirements are lowered. Downtime prices decrease.
Coke calcining rotating kilns operate in severe heat. They refine petroleum coke into calcined coke. Calcined coke is important for light weight aluminum smelting. These kilns endure extreme temperature levels daily. They deal with the abrasive coke product well. Built challenging, they last long under stress. The calcining procedure is reliable and comprehensive. Output fulfills stringent industry specs. Reliability is essential for continuous operation.
These kilns provide distinctive benefits. The limestone kiln conserves substantial energy. The plaster kiln makes certain consistent powder top quality. The coke calcining kiln supplies robust, dependable efficiency. Each style addresses details product challenges. They deliver effective thermal handling. Decreased gas usage lowers environmental influence. Reduced upkeep needs save money. Consistent product quality constructs trust fund. These aspects make them smart industrial financial investments.
Company Introduction
Established in 2001, plant Machinery Equipment Co.,ltd. focus on metal research and mining machinery spare parts. 2 factories over an area of 13,300 square meters, based on 100+ sets of equipment, our production capacity reaches 12000 Tons/Year. has passed ISO 9001 quality managment system certification in 2008.
Our mainly products are dragline excavator spare parts,rotary kiln spare parts, large modulus gear (gear shaft), gearbox ect. 40+ patents with over 45 years experience to help focus on improve the service life of spare parts. We belive that more than 80% reason of mechanical parts’ working life depends on hot processing (steel making/forging/casting/welding/heat treatment). Eight material engineers will control the quality from the original resource.
If you are interested, please feel free to contact us.
Payment
L/C, T/T, Western Union, Paypal, Credit Card etc.
Shipment
By sea, by air, by express, as customers request.
5 FAQs of Direct Energy Saving Limestone Rotary Kiln Gypsum Production Line Rotary Kiln Coke Calcining Rotary Kiln
What are rotary kilns used for in these production lines?
Rotary kilns heat materials at high temperatures. The direct energy saving limestone kiln makes quicklime from limestone. The gypsum kiln produces stucco for plasterboard. The coke calcining kiln turns petroleum coke into calcined coke for aluminum smelting.
How does the direct energy saving limestone rotary kiln save energy?
It uses thick insulation to trap heat. A preheater warms raw limestone using hot exhaust gases. A cooler recovers heat from finished quicklime. This recycled heat cuts fuel needs. Less fuel means lower costs.
What are the main parts of a gypsum production line rotary kiln?
The kiln shell is a long steel cylinder. Refractory bricks line the inside to handle heat. Support rollers keep the kiln turning smoothly. Seals prevent heat leaks. A drive system controls rotation speed.
Why is coke calcining important? How does the rotary kiln handle it?
Calcining removes impurities from petroleum coke. Pure coke is vital for aluminum production. The rotary kiln heats coke to 1200-1350°C. This burns off volatile chemicals. The result is strong, carbon-rich calcined coke.
What maintenance keeps these rotary kilns running well?
Check refractory linings monthly for cracks. Replace worn bricks quickly. Lubricate rollers and bearings weekly. Clean dust from seals and joints. Monitor temperature gauges daily. Fix small problems before they worsen.
( Direct Energy Saving Limestone Rotary Kiln Gypsum Production Line Rotary Kiln Coke Calcining Rotary Kiln)
REQUEST A QUOTE
RELATED PRODUCTS
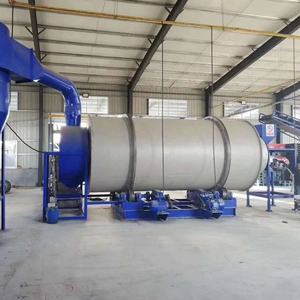
High-Temperature Stainless Steel Head for Large Diameter Boiler Accessories Casting Technics
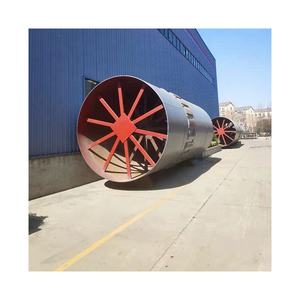
Yogie Energy rotary Dryer Drum rotary kiln Shell For Cement Making Machinery Plant
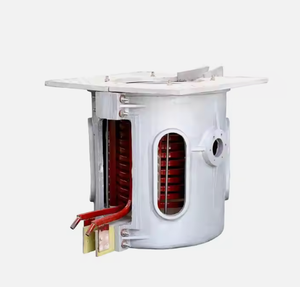
clinker calcining rotary kiln rotary calciner for industrial powder rotary calciner equipment
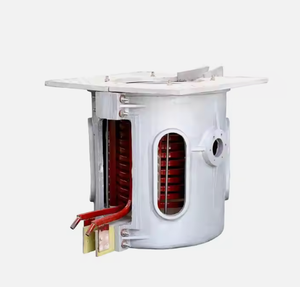
Best Energy-saving Rotary Dryer Furnace Kiln for Chemical/mining metallurgy Rotary Kiln
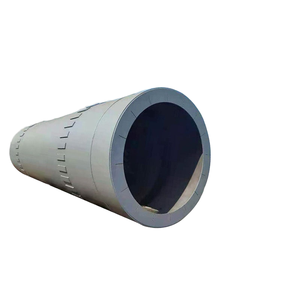
220v 380v Industrial Electric Screw Barrel Band Heater Element Ceramic Coil For Plastic Mould Machine
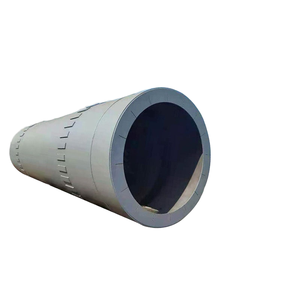