PRODUCT PARAMETERS
Description
Introduction of New Construction Rotational Kiln Rotary Kiln Wheel Block Custom Processing Lime Zinc Oxide Aluminum Ash Roasting Aluminum Ash
A rotary kiln is a kind of industrial equipment used for material heating and processing, which is widely used in cement, metallurgy, chemical industry, etc. New Construction Rotational Kiln Rotary Kiln Wheel Block Custom Processing Lime Zinc Oxide Aluminum Ash Roasting Aluminum Ash refers to various parts and components which are necessary for maintaining and repairing the normal operation of the rotary kiln, such as cylinder, baffle wheel, pallet, sealing device and so on.
Features and advantages of New Construction Rotational Kiln Rotary Kiln Wheel Block Custom Processing Lime Zinc Oxide Aluminum Ash Roasting Aluminum Ash
High-temperature resistance: Due to the extremely high temperature of the working environment of the rotary kiln, the spare parts are usually made of refractory materials or special alloys to ensure that they can work stably under high temperatures.
High abrasion resistance: Long time material friction and chemical erosion require spare parts to have excellent abrasion resistance to prolong service life.
High structural strength: in order to withstand heavy loads and the pressure of continuous operation, the design of spare parts will place special emphasis on structural strength and reliability.
Easy to install and maintain: Considering the need for frequent replacement, many spare parts are designed to be simpler and easier for quick installation and maintenance.
Strong adaptability: different industries have different needs for rotary kilns, so spare parts need to have good versatility and adaptability to meet diverse application conditions.
(New Construction Rotational Kiln Rotary Kiln Wheel Block Custom Processing Lime Zinc Oxide Aluminum Ash Roasting Aluminum Ash)
Specifications of New Construction Rotational Kiln Rotary Kiln Wheel Block Custom Processing Lime Zinc Oxide Aluminum Ash Roasting Aluminum Ash
The brand-new building and construction rotational kiln rotating kiln wheel block is constructed for sturdy commercial handling. It manages materials like lime, zinc oxide, and light weight aluminum ash. The design focuses on performance, durability, and personalization. The kiln runs at high temperatures, guaranteeing comprehensive roasting and calcination.
The kiln’s main body makes use of top-quality steel. It withstands warmth, wear, and deterioration. The temperature level range reaches up to 1450 ° C. This suits demanding processes like light weight aluminum ash roasting. The revolving drum ensures even warmth distribution. Product high quality remains regular.
Custom-made wheel blocks assistance the kiln’s structure. They adapt to particular lots demands. Customers pick sizes and arrangements. Wheel blocks decrease friction during turning. This reduces energy usage and maintenance requirements. The kiln’s diameter varies from 1.5 meters to 4.5 meters. Length ranges 8 meters and 50 meters. Custom sizing fits different manufacturing scales.
Handling lime entails accurate temperature control. The kiln’s insulation reduces heat loss. Fuel efficiency enhances. Zinc oxide manufacturing needs stable rotation speeds. Flexible drives enable fine-tuning. Aluminum ash roasting requires quick heating cycles. The kiln’s heater system reacts promptly.
Advanced sealing prevents gas leakages. Exhausts fulfill ecological criteria. Operators adjust air movement and pressure quickly. Safety and security functions consist of overheating informs and emergency stops. Automated systems minimize hands-on treatment. Sensing units keep an eye on temperature, rate, and pressure in actual time.
The kiln’s interior lining usages refractory bricks or ceramic fiber. These materials manage extreme warmth. Substitute periods extend. Upkeep expenses remain reduced. Drive systems consist of gearboxes and electric motors from trusted brands. Power transmission continues to be dependable.
Customized processing alternatives cover feed mechanisms, discharge configurations, and cooling systems. Customers incorporate the kiln into existing assembly line. Compatibility with complementary devices is guaranteed. Technical assistance covers installment, screening, and training.
The kiln matches sectors such as metallurgy, chemicals, and construction. It processes basic materials into high-purity products. Outcome high quality satisfies international criteria. Manufacturing ability scales from tiny sets to continuous procedures. Distribution times depend on personalization levels. Producers give comprehensive specs upon demand.
(New Construction Rotational Kiln Rotary Kiln Wheel Block Custom Processing Lime Zinc Oxide Aluminum Ash Roasting Aluminum Ash)
Applications of New Construction Rotational Kiln Rotary Kiln Wheel Block Custom Processing Lime Zinc Oxide Aluminum Ash Roasting Aluminum Ash
The new construction rotational kiln rotating kiln wheel block customized processing uses flexible solutions for industrial thermal handling. This innovation manages lime production effectively. The rotating kiln framework sustains high-temperature calcination. It transforms sedimentary rock into quicklime properly. The personalized wheel block style makes sure smooth rotation under heavy tons. It decreases mechanical stress throughout operation. The system benefits zinc oxide handling. It handles regulated home heating environments. This enables specific disintegration of zinc ore. The outcome is high-purity zinc oxide. The kiln’s adjustable rate and temperature level setups match specific material demands. Light weight aluminum ash roasting take advantage of this kiln’s layout. The process recovers important steels from industrial waste. The rotary motion advertises even warmth circulation. This prevents material clumping. The custom wheel obstructs use heat-resistant alloys. They endure extended exposure to harsh byproducts. The kiln’s modular arrangement permits easy scaling. Industries readjust ability based on manufacturing demands. The lime handling application sustains building and steel manufacturing. Regular outcome quality satisfies stringent market criteria. Zinc oxide production offers rubber and ceramic industries. The kiln’s precision ensures ideal chemical structure. Aluminum ash roasting addresses environmental concerns. It reduces waste volume. It recoups multiple-use light weight aluminum web content. The custom wheel blocks undertake strenuous testing. They adjust to various kiln dimensions and material kinds. Maintenance demands remain reduced because of long lasting parts. Operators save time on repairs. Power effectiveness enhances with enhanced heat retention. Gas expenses go down without compromising result. The kiln matches little and big facilities. It incorporates with existing assembly line. Personalized handling choices deal with unique industrial challenges. Each part gets customized for certain thermal accounts. Product handling becomes much safer and much faster. The style decreases heat loss. Processing times shorten. Product consistency increases throughout batches. This modern technology fulfills demands for sustainability. It takes full advantage of source healing. It sustains diverse manufacturing sectors with trusted efficiency.
Company Introduction
Established in 2001, plant Machinery Equipment Co.,ltd. focus on metal research and mining machinery spare parts. 2 factories over an area of 13,300 square meters, based on 100+ sets of equipment, our production capacity reaches 12000 Tons/Year. has passed ISO 9001 quality managment system certification in 2008.
Our mainly products are dragline excavator spare parts,rotary kiln spare parts, large modulus gear (gear shaft), gearbox ect. 40+ patents with over 45 years experience to help focus on improve the service life of spare parts. We belive that more than 80% reason of mechanical parts’ working life depends on hot processing (steel making/forging/casting/welding/heat treatment). Eight material engineers will control the quality from the original resource.
If you are interested, please feel free to contact us.
Payment
L/C, T/T, Western Union, Paypal, Credit Card etc.
Shipment
By sea, by air, by express, as customers request.
5 FAQs of New Construction Rotational Kiln Rotary Kiln Wheel Block Custom Processing Lime Zinc Oxide Aluminum Ash Roasting Aluminum Ash
New Construction Rotational Kiln Rotary Kiln Wheel Block Custom Processing Lime Zinc Oxide Aluminum Ash Roasting Aluminum Ash FAQs
What is a rotational kiln?
A rotational kiln is a large heating machine used to process materials at high temperatures. It rotates materials inside a long cylindrical chamber. This process helps in chemical reactions or physical changes. The rotary kiln wheel block supports the kiln’s rotation. It ensures smooth movement during operations like lime calcination or aluminum ash roasting.
What industries use this rotary kiln?
This kiln is used in industries like steel, cement, and chemical manufacturing. It processes lime, zinc oxide, and aluminum ash. The kiln handles materials needing high-temperature treatment. Factories use it for roasting, drying, or decomposing raw materials. It works for small and large-scale production.
How is the rotary kiln customized?
Customization depends on material type, production goals, and site conditions. The kiln’s size, heating temperature, and rotation speed are adjustable. The wheel block design can be modified for better load distribution. Custom processing ensures the kiln fits specific needs like zinc oxide refining or aluminum ash recycling.
What maintenance does the kiln require?
Regular checks on the wheel blocks, gears, and heating elements are essential. Lubricate moving parts to reduce friction. Inspect the kiln lining for wear every 3–6 months. Clean residue from previous batches to prevent contamination. Proper maintenance extends the kiln’s lifespan and avoids downtime.
Are there safety features in the kiln design?
Yes. The kiln includes temperature sensors, pressure relief valves, and emergency stop systems. These prevent overheating or mechanical failures. The wheel block is built to handle heavy loads without deformation. Operators receive safety guidelines to manage high-temperature risks. Regular training ensures safe handling during roasting or cooling processes.
(New Construction Rotational Kiln Rotary Kiln Wheel Block Custom Processing Lime Zinc Oxide Aluminum Ash Roasting Aluminum Ash)
REQUEST A QUOTE
RELATED PRODUCTS
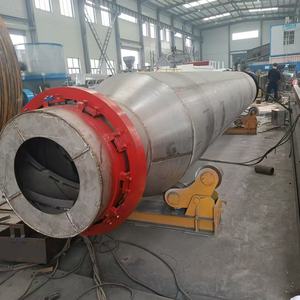
Large Wheel Large Diameter Spur Gear High Quality Cnc Machining Rotary Kiln Big Wheel
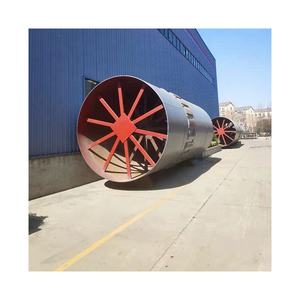
High Temperature Kiln Muffle Oven Lab 1100 1200 1400 1500 1600 1700 1800 Degree Electric Ceramic Box Melting Muffle Furnace
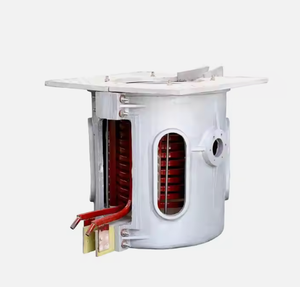
Industrial Calcination Rotary Kiln For Kaolin
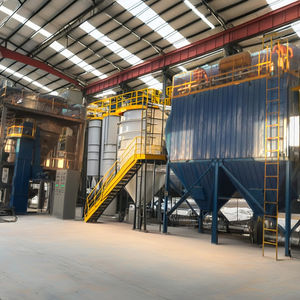
Rotary Kiln/ Zinc Oxide Production Line Rotary Kiln
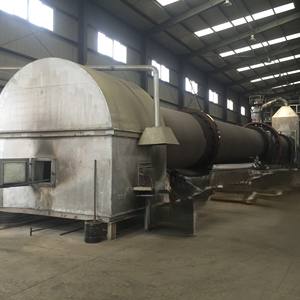
bauxite periodic rotary kiln cement 1000c cement kiln cooling fan and spare parts rotary valve for kiln machine
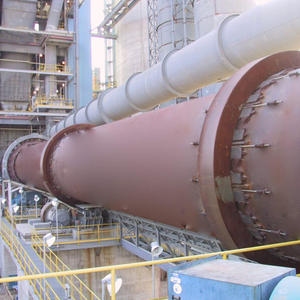