PRODUCT PARAMETERS
Description
Introduction of Rotary Kiln Shaft kiln Iron Technology Iron Ore Oxide Pelletizing Plant Iron Ore Pellet Plant
A rotary kiln is a kind of industrial equipment used for material heating and processing, which is widely used in cement, metallurgy, chemical industry, etc. Rotary Kiln Shaft kiln Iron Technology Iron Ore Oxide Pelletizing Plant Iron Ore Pellet Plant refers to various parts and components which are necessary for maintaining and repairing the normal operation of the rotary kiln, such as cylinder, baffle wheel, pallet, sealing device and so on.
Features and advantages of Rotary Kiln Shaft kiln Iron Technology Iron Ore Oxide Pelletizing Plant Iron Ore Pellet Plant
High-temperature resistance: Due to the extremely high temperature of the working environment of the rotary kiln, the spare parts are usually made of refractory materials or special alloys to ensure that they can work stably under high temperatures.
High abrasion resistance: Long time material friction and chemical erosion require spare parts to have excellent abrasion resistance to prolong service life.
High structural strength: in order to withstand heavy loads and the pressure of continuous operation, the design of spare parts will place special emphasis on structural strength and reliability.
Easy to install and maintain: Considering the need for frequent replacement, many spare parts are designed to be simpler and easier for quick installation and maintenance.
Strong adaptability: different industries have different needs for rotary kilns, so spare parts need to have good versatility and adaptability to meet diverse application conditions.
(Rotary Kiln Shaft kiln Iron Technology Iron Ore Oxide Pelletizing Plant Iron Ore Pellet Plant)
Specifications of Rotary Kiln Shaft kiln Iron Technology Iron Ore Oxide Pelletizing Plant Iron Ore Pellet Plant
Rotary kiln shaft kiln iron modern technology plants make iron ore oxide pellets. These pellets work well in blast furnaces or straight decrease processes. The plant uses a rotary kiln and a shaft furnace together. This mix gives high efficiency and good item quality.
Raw iron ore concentrate gets here first. Workers mix it very carefully with binders like bentonite. After that the mixture gets in a balling drum or disc pelletizer. Tiny eco-friendly balls develop throughout this action. These environment-friendly rounds determine regarding 6 to 16 millimeters across. They are still moist and breakable.
The eco-friendly spheres take a trip to a grate machine. Warm gases blow with them below. This step dries out the balls extensively. It also preheats them for the following phase. More powerful pellets arise from this drying out and preheating.
Next comes the rotating kiln. The pellets roll slowly inside this lengthy, revolving cylinder. Temperatures get to 1200 to 1350 levels Celsius inside. This extreme warmth triggers chain reactions. The iron ore oxide changes into a solidified pellet kind. The kiln turns continually. This makes sure every pellet gets warmed evenly.
Warm pellets exit the rotary kiln. They move straight into the shaft heater. The shaft heating system cools the pellets gradually. Managed cooling protects against fractures. It secures the pellet toughness. Cooled pellets are tough sufficient for managing and transport. They are ready for steelmaking.
The entire system requires exact temperature control. Sensors keep an eye on warm levels continuously. Operators readjust fuel and air circulation to preserve precise problems. Good control implies constant pellet top quality.
Modern plants concentrate on energy conserving. They record waste warm from the kiln and heating system. This heat typically pre-heats burning air or dries basic materials. It reduces total fuel costs. Emission control systems are additionally vital. They cleanse exhaust gases prior to release.
Pellet size harmony matters considerably. Regular sizing makes sure smooth furnace procedure later. Evaluating eliminates extra-large or undersized pellets. Just properly sized pellets continue to storage. Plants go for high result prices. Normal capabilities vary from thousands of thousands to numerous bunches yearly. Integrity is vital for continual manufacturing. Normal maintenance maintains equipment running well.
(Rotary Kiln Shaft kiln Iron Technology Iron Ore Oxide Pelletizing Plant Iron Ore Pellet Plant)
Applications of Rotary Kiln Shaft kiln Iron Technology Iron Ore Oxide Pelletizing Plant Iron Ore Pellet Plant
Iron ore pelletizing plants transform iron ore fines right into strong, consistent pellets. These pellets boost blast heating system efficiency substantially. Shaft kilns and rotary kilns are core modern technologies for this process. Plants use both to achieve top quality pellets successfully.
First, raw iron ore fines come to the plant. They obtain combined with binders like bentonite clay. This mixture goes into a balling drum or disc. Right here, it rolls right into tiny, environment-friendly spheres called eco-friendly pellets. These eco-friendly pellets are soft and contain wetness. They require setting for transport and smelting. This hardening step is called induration. This is where the kilns run.
Shaft kilns are tall, upright furnaces. Eco-friendly pellets move downward via the shaft. Warm gases flow upwards. This counter-current circulation warms the pellets slowly. It dries them initially. Then it preheats them. Ultimately, it solidifies them at high temperatures. Shaft kilns supply great thermal effectiveness. They have a smaller physical footprint in some cases. Managing gas circulation precisely is vital for consistent pellet quality.
Rotating kilns are long, a little inclined cylinders. They turn gradually. Environment-friendly pellets traveling from the higher end to the reduced end. Hot gases circulation along the kiln. This warms the pellets as they tumble. The rolling activity guarantees even home heating. Rotating kilns deal with a wide variety of feed products well. They offer outstanding temperature control throughout the pellet. This results in regular metallurgical homes.
Both kiln kinds bake the pellets at really high warmth. This burns off the binder. It additionally causes the iron oxide particles to fuse together. The outcome is strong, long lasting iron ore pellets. These pellets have high iron material. They have uniform size. They resist destruction during handling and shipping. Steel mills favor these pellets. They thaw equally in blast furnaces. They boost heater productivity. They minimize coke intake. They also lower overall exhausts per ton of steel created. The kiln modern technology is crucial for modern-day, reliable ironmaking.
Company Introduction
Established in 2001, plant Machinery Equipment Co.,ltd. focus on metal research and mining machinery spare parts. 2 factories over an area of 13,300 square meters, based on 100+ sets of equipment, our production capacity reaches 12000 Tons/Year. has passed ISO 9001 quality managment system certification in 2008.
Our mainly products are dragline excavator spare parts,rotary kiln spare parts, large modulus gear (gear shaft), gearbox ect. 40+ patents with over 45 years experience to help focus on improve the service life of spare parts. We belive that more than 80% reason of mechanical parts’ working life depends on hot processing (steel making/forging/casting/welding/heat treatment). Eight material engineers will control the quality from the original resource.
If you are interested, please feel free to contact us.
Payment
L/C, T/T, Western Union, Paypal, Credit Card etc.
Shipment
By sea, by air, by express, as customers request.
5 FAQs of Rotary Kiln Shaft kiln Iron Technology Iron Ore Oxide Pelletizing Plant Iron Ore Pellet Plant
Here are five common questions about Rotary Kiln Shaft Kiln Iron Technology for Iron Ore Pellet Plants:
What exactly does this Rotary Kiln Shaft Kiln Technology do?
This technology processes iron ore concentrate. It turns fine powder into strong, usable pellets. The pellets are needed for blast furnaces or direct reduction plants to make iron. The process heats the material very high. This makes the pellets hard and stable.
Why pick this over other pelletizing methods?
The shaft kiln part gives big advantages. It uses less fuel. The heat transfers better inside the shaft. The system needs less space. Operating costs are often lower. Pellet quality stays consistent. This makes it a smart choice financially.
How does the shaft kiln actually work?
The shaft kiln is a tall, vertical furnace. Green pellets enter from the top. Hot gases rise from the bottom. The pellets move slowly down. They meet the rising hot gases. This heats them evenly. The pellets harden as they descend. Finished pellets exit the bottom.
What are the main benefits for the pellet plant?
Efficiency is key. The design saves energy. Fuel consumption drops significantly. The plant footprint is smaller. That saves space and construction cost. Operations are simpler to control. Pellet strength and quality are reliably high. This leads to better furnace performance later.
What makes pellets good using this method?
The controlled heating is crucial. The pellets achieve the right hardness. They resist breaking during handling and transport. They also have excellent metallurgical properties. This means they work better inside the furnace. Smelting becomes more efficient. Less waste happens.
(Rotary Kiln Shaft kiln Iron Technology Iron Ore Oxide Pelletizing Plant Iron Ore Pellet Plant)
REQUEST A QUOTE
RELATED PRODUCTS
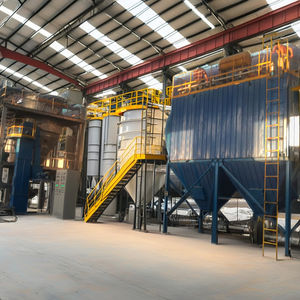
For LIEBHERR PR722 LITRONIC segment group bulldozer spare parts
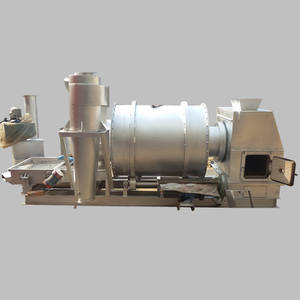
Professional rotary kiln spare parts steel plate/roller/refractory bricks rotary kiln
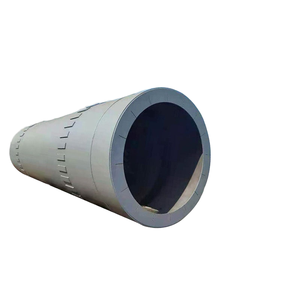
Cement plant Large Diameter Casting girth gear Alloy Steel Rotary Kiln Large Module Half Ring Gear
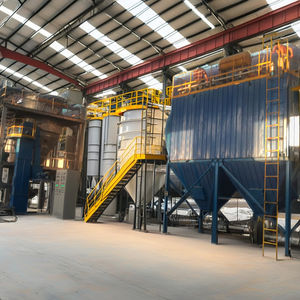
OEM ODM Large Heavy-Duty Rotary Kiln Dryer Factory High Quality Carbon Steel Girth Spur Large Ring Gear Machining Services
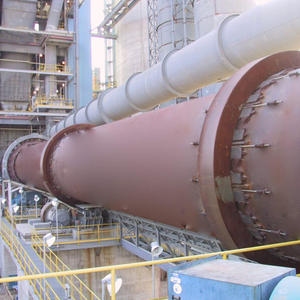
Low Rotary Kiln Spare Parts Supporting Roller Assembly /High Quality Supporting Roller Assembly Of Kaolin Burning Plant
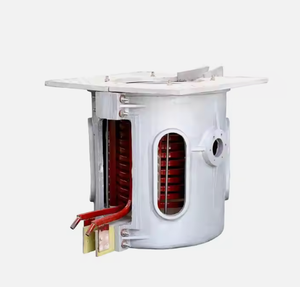