PRODUCT PARAMETERS
Description
Introduction of Rotary Kiln/ Zinc Oxide Production Line Rotary Kiln
A rotary kiln is a kind of industrial equipment used for material heating and processing, which is widely used in cement, metallurgy, chemical industry, etc. Rotary Kiln/ Zinc Oxide Production Line Rotary Kiln refers to various parts and components which are necessary for maintaining and repairing the normal operation of the rotary kiln, such as cylinder, baffle wheel, pallet, sealing device and so on.
Features and advantages of Rotary Kiln/ Zinc Oxide Production Line Rotary Kiln
High-temperature resistance: Due to the extremely high temperature of the working environment of the rotary kiln, the spare parts are usually made of refractory materials or special alloys to ensure that they can work stably under high temperatures.
High abrasion resistance: Long time material friction and chemical erosion require spare parts to have excellent abrasion resistance to prolong service life.
High structural strength: in order to withstand heavy loads and the pressure of continuous operation, the design of spare parts will place special emphasis on structural strength and reliability.
Easy to install and maintain: Considering the need for frequent replacement, many spare parts are designed to be simpler and easier for quick installation and maintenance.
Strong adaptability: different industries have different needs for rotary kilns, so spare parts need to have good versatility and adaptability to meet diverse application conditions.
(Rotary Kiln/ Zinc Oxide Production Line Rotary Kiln)
Specifications of Rotary Kiln/ Zinc Oxide Production Line Rotary Kiln
Rotating kilns for zinc oxide manufacturing process zinc focuses or various other zinc-bearing materials. These kilns are huge, revolving steel cylinders. They are somewhat likely. Product gets in the greater end. Warm is used at the reduced end. The material gradually relocates down towards the warm resource. This movement ensures complete mixing and chemical reactions.
Common kiln sizes range from 40 meters to over 100 meters. Sizes normally fall in between 2.5 meters and 4.5 meters. The specific dimension depends on the necessary production capability. Larger kilns deal with more material per hour. Production capabilities vary extensively. They can be from 20 loads daily approximately 200 loads each day or more. Temperature control is vital. Running temperature levels inside the kiln reach between 1000 ° C and 1450 ° C. This high heat repel volatile parts. It transforms zinc compounds into zinc oxide vapor.
The kiln shell is robust carbon steel. Thick steel plates make certain architectural honesty. The inside is lined with special refractory bricks. These blocks endure severe warmth and chemical strike. Various refractory types match different kiln zones. Drive systems revolve the kiln. They make use of durable transmissions and effective electric motors. Turning speeds are adjustable. Speeds are normally low, around 0.5 to 2.0 revolutions per minute. This slow-moving turning permits proper product handling.
Kilns can use different fuels. Common alternatives include natural gas, heavy oil, crushed coal, or producer gas. Heaters are positioned at the discharge end. They supply the needed extreme warmth. Seals protect against air leak at both ends. This preserves the called for ambience inside. Reliable dirt collection systems record zinc oxide fume exiting the kiln. Modern plants integrate innovative procedure control systems. These systems monitor temperature, stress, feed price, and rotation rate. They optimize efficiency and product quality.
(Rotary Kiln/ Zinc Oxide Production Line Rotary Kiln)
Applications of Rotary Kiln/ Zinc Oxide Production Line Rotary Kiln
Rotary kilns deal with zinc oxide production well. This procedure starts with zinc ore concentrate. People often make use of willemite ore. The kiln warms this product intensely. This heating step is called calcination. It gets rid of unwanted components. The kiln is a long, somewhat tilted steel cylinder. It rotates gradually. Workers feed the ore concentrate into the higher end. The rotation moves the material down in the direction of the hotter, reduced end. Heat comes from heaters. These heaters fire into the kiln’s lower area. Temperatures climb up extremely high inside. They get to over 1000 degrees Celsius. This intense warm causes chain reactions. Unpredictable components like cadmium and lead evaporate first. They leave the solid product. After that the main response occurs. The zinc in the ore reacts chemically. It develops into zinc oxide vapor. This vapor takes a trip with the hot gases. It moves towards the kiln’s top end. The gases exit the kiln. They enter into air conditioning and collection systems. Unique bag filters or condensers catch the zinc oxide particles. This gathered powder is the final zinc oxide product. It is really pure. The staying solid material departures the kiln’s lower end. This residue is clinker. Workers remove this clinker for disposal or other usages. The rotary kiln style gives excellent blending. It ensures all material obtains enough heat. This is important for complete response. Excellent temperature level control is essential. Operators handle the burner setups thoroughly. They enjoy the material flow. Constant rotation keeps the procedure consistent. This approach accurately makes high-grade zinc oxide. Factories value its efficiency and robustness. The kiln takes care of continual operation well. This makes large production feasible.
Company Introduction
Established in 2001, plant Machinery Equipment Co.,ltd. focus on metal research and mining machinery spare parts. 2 factories over an area of 13,300 square meters, based on 100+ sets of equipment, our production capacity reaches 12000 Tons/Year. has passed ISO 9001 quality managment system certification in 2008.
Our mainly products are dragline excavator spare parts,rotary kiln spare parts, large modulus gear (gear shaft), gearbox ect. 40+ patents with over 45 years experience to help focus on improve the service life of spare parts. We belive that more than 80% reason of mechanical parts’ working life depends on hot processing (steel making/forging/casting/welding/heat treatment). Eight material engineers will control the quality from the original resource.
If you are interested, please feel free to contact us.
Payment
L/C, T/T, Western Union, Paypal, Credit Card etc.
Shipment
By sea, by air, by express, as customers request.
5 FAQs of Rotary Kiln/ Zinc Oxide Production Line Rotary Kiln
Here are five common questions about rotary kilns for zinc oxide production:
What does this rotary kiln actually do?
It turns zinc ore into zinc oxide powder. The kiln heats zinc concentrate very hot. This process removes impurities. We call this calcination. The result is high-purity zinc oxide powder ready for use.
How does the kiln work?
The kiln is a long, slightly tilted steel cylinder. It rotates slowly. Zinc ore moves from the higher end down to the lower end. Hot gases flow the opposite way. The ore gets heated gradually as it travels. Chemical reactions happen inside. Zinc oxide forms before the material exits.
What are the main parts of the production line?
The core is the rotating kiln itself. Feeders put the raw ore in at one end. A burner provides the intense heat needed. Dust collectors capture fine powder from the exhaust gases. Coolers bring the hot zinc oxide down to a safe temperature. Conveyors move material between stages.
Why is temperature control so important?
The chemical reactions need precise heat. Too low, the reactions won’t finish. Impurities stay. Too high, you damage the kiln lining or waste energy. The ideal temperature is usually around 1000°C inside the reaction zone. Good control ensures pure zinc oxide and protects the equipment.
What maintenance is required regularly?
Check the kiln’s refractory bricks often. They line the inside and take the heat. Look for wear or cracks. Inspect the shell for warping or damage. Monitor the drive system and support rollers. Keep seals tight to prevent air leaks. Clean dust collection systems frequently. Consistent checks prevent big problems.
(Rotary Kiln/ Zinc Oxide Production Line Rotary Kiln)
REQUEST A QUOTE
RELATED PRODUCTS
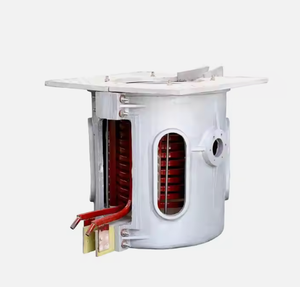
Industrial Calcination Rotary Kiln For Kaolin
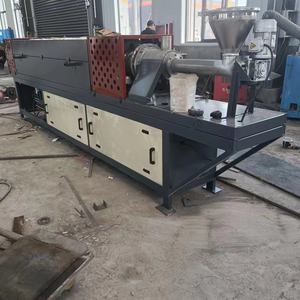
Hot Recently Double Firing Frit For Daily Ceramics Magnesia Porcelain Second Firing Electric kiln Glaze Firing
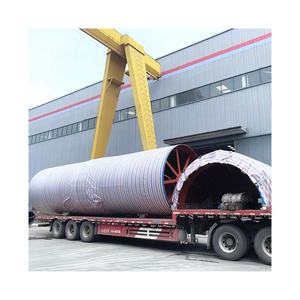
custom ball mill casting ZG310-570 42CrMo steel rotary kiln external spur tooth large ring gear
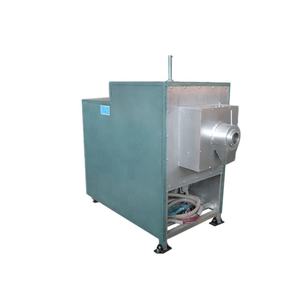
large module ring gear cement ball mill big spur girth wheel outer ring gear casting rotary kiln large girth gear
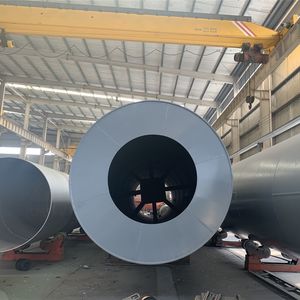
Rotary Kiln Spare Part Kiln Sealing/Big Gear Ring/Support Roller
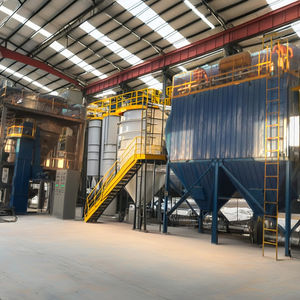