PRODUCT PARAMETERS
Description
Introduction of Energy saving rotary kiln calcining a variety of materials production line zinc oxide desulfurization gypsum kaolin chromium
A rotary kiln is a kind of industrial equipment used for material heating and processing, which is widely used in cement, metallurgy, chemical industry, etc. Energy saving rotary kiln calcining a variety of materials production line zinc oxide desulfurization gypsum kaolin chromium refers to various parts and components which are necessary for maintaining and repairing the normal operation of the rotary kiln, such as cylinder, baffle wheel, pallet, sealing device and so on.
Features and advantages of Energy saving rotary kiln calcining a variety of materials production line zinc oxide desulfurization gypsum kaolin chromium
High-temperature resistance: Due to the extremely high temperature of the working environment of the rotary kiln, the spare parts are usually made of refractory materials or special alloys to ensure that they can work stably under high temperatures.
High abrasion resistance: Long time material friction and chemical erosion require spare parts to have excellent abrasion resistance to prolong service life.
High structural strength: in order to withstand heavy loads and the pressure of continuous operation, the design of spare parts will place special emphasis on structural strength and reliability.
Easy to install and maintain: Considering the need for frequent replacement, many spare parts are designed to be simpler and easier for quick installation and maintenance.
Strong adaptability: different industries have different needs for rotary kilns, so spare parts need to have good versatility and adaptability to meet diverse application conditions.
(Energy saving rotary kiln calcining a variety of materials production line zinc oxide desulfurization gypsum kaolin chromium)
Specifications of Energy saving rotary kiln calcining a variety of materials production line zinc oxide desulfurization gypsum kaolin chromium
The energy-saving rotary kiln calcining assembly line processes products like zinc oxide, desulfurization plaster, kaolin, and chromium substances. It incorporates high performance with reduced energy use. The kiln utilizes innovative insulation products to minimize warm loss. It integrates heat recovery systems to recycle excess thermal energy. This design cuts energy intake by approximately 30% compared to conventional designs. The assembly line deals with multiple materials without needing significant modifications. It helps zinc oxide calcination in chemical production. It refines desulfurization plaster into construction-grade items. It deals with kaolin for porcelains and paper markets. It takes care of chromium substances for metallurgical applications. The kiln runs at temperatures in between 800 ° C and 1400 ° C. The temperature level variety fits varied material demands. A variable-speed electric motor controls rotational rate. Readjusting rate optimizes product retention time. This guarantees extensive calcination and consistent product top quality. The system uses automated controls for exact monitoring. Sensing units track temperature level, pressure, and air movement in actual time. Operators change specifications via a main PLC interface. This lowers manual treatment. Maintenance demands are very little. The kiln’s refractory lining stands up to heats and chemical rust. Long lasting building materials expand equipment lifespan. Safety and security features include emergency situation air conditioning systems. Pressure relief valves protect against functional dangers. The assembly line satisfies environmental standards. Emissions remain below regulated limitations. Dust enthusiasts catch particle matter. Gas scrubbers neutralize harmful fumes. Waste warmth powers supporting processes. This reduces total carbon footprint. Energy-saving advantages reduce operational expenses. Steady thermal performance makes certain high result prices. The layout reduces warmth waste throughout material transfer. Uniform home heating stops product problems. It matches continual or set handling. Customizable arrangements fit particular manufacturing ranges. The rotary kiln system benefits little manufacturing facilities or large plants. Installment calls for standard foundation assistance. Training covers standard operation and troubleshooting. Technical assistance is offered for maintenance. The equipment is compatible with existing production configurations. Upgrading to this system enhances sustainability. It maintains efficiency while cutting power usage.
(Energy saving rotary kiln calcining a variety of materials production line zinc oxide desulfurization gypsum kaolin chromium)
Applications of Energy saving rotary kiln calcining a variety of materials production line zinc oxide desulfurization gypsum kaolin chromium
Energy-saving rotating kilns are extensively used in refining various products. These systems take care of zinc oxide, desulfurization plaster, kaolin, and chromium successfully. They reduce power usage while keeping high efficiency. This makes them a practical choice for industrial operations.
Zinc oxide production take advantage of rotating kilns. The kilns heat zinc-containing products at controlled temperatures. This procedure eliminates pollutants and develops high-purity zinc oxide. The energy-saving style cuts gas intake. It additionally decreases emissions. Industries like porcelains and rubber depend on this approach for high quality zinc oxide.
Desulfurization plaster reusing uses these kilns. Power plants produce plaster as a by-product. The kiln heats it to remove dampness and convert it into multiple-use plaster. This decreases waste. It supports lasting practices. The calcined plaster is utilized in building and construction products like drywall. Energy performance right here decreases operational expenses.
Kaolin processing relies on rotating kilns. Kaolin is a clay mineral utilized in paper, paint, and cosmetics. The kiln removes pollutants via calcination. This enhances illumination and physical residential properties. The energy-saving feature makes certain even heating. It stops overheating. This keeps item top quality while conserving power.
Chromium ore therapy is an additional essential application. Chromium substances are poisonous if not taken care of effectively. Rotating kilns securely process chromium ore at high temperatures. This stabilizes unsafe components. It prevents ecological contamination. The kiln’s layout enables exact temperature control. This makes sure risk-free, effective handling. Recouping chromium from waste materials is also feasible.
These kilns adapt to different products quickly. Their modular design sustains customization. Industries value the reduced energy prices and ecological effect. The systems operate continually. They call for very little upkeep. This improves performance. Advanced warm recovery innovation additionally improves effectiveness. It recycles waste warmth from the procedure.
Rotary kilns meet strict environmental requirements. They cut greenhouse gas exhausts. They additionally lower energy use compared to typical approaches. This straightens with international sustainability objectives. Services acquire both economic and eco-friendly advantages. The adaptability of these kilns makes them crucial in modern product handling.
Company Introduction
Established in 2001, plant Machinery Equipment Co.,ltd. focus on metal research and mining machinery spare parts. 2 factories over an area of 13,300 square meters, based on 100+ sets of equipment, our production capacity reaches 12000 Tons/Year. has passed ISO 9001 quality managment system certification in 2008.
Our mainly products are dragline excavator spare parts,rotary kiln spare parts, large modulus gear (gear shaft), gearbox ect. 40+ patents with over 45 years experience to help focus on improve the service life of spare parts. We belive that more than 80% reason of mechanical parts’ working life depends on hot processing (steel making/forging/casting/welding/heat treatment). Eight material engineers will control the quality from the original resource.
If you are interested, please feel free to contact us.
Payment
L/C, T/T, Western Union, Paypal, Credit Card etc.
Shipment
By sea, by air, by express, as customers request.
5 FAQs of Energy saving rotary kiln calcining a variety of materials production line zinc oxide desulfurization gypsum kaolin chromium
What materials can the energy-saving rotary kiln process?
The kiln handles zinc oxide, desulfurization gypsum, kaolin, chromium compounds, and similar materials. It supports multiple industries like metallurgy, chemicals, construction. The design allows switching between materials without major adjustments.
How does the kiln save energy?
Advanced insulation traps heat inside. A heat recovery system reuses hot gases from the process. Lower fuel consumption cuts operational costs. The kiln’s structure reduces heat loss. This makes it more efficient than traditional models.
Can the kiln handle different materials in one production line?
Yes. Adjustable temperature zones and rotation speeds adapt to material needs. Operators control settings for each material’s calcination requirements. This flexibility supports mixed production lines. Downtime between material changes is minimal.
What maintenance does the kiln need?
Regular checks on seals, insulation, and heating elements prevent issues. Lubricate moving parts weekly. Replace worn components like refractory linings based on usage. Automated monitoring systems alert users to potential problems early.
Does the kiln reduce environmental impact?
Lower emissions result from efficient fuel use. Waste gases pass through filters before release. The process minimizes harmful byproducts. Recycling heat cuts overall energy demand. This meets strict environmental standards.
(Energy saving rotary kiln calcining a variety of materials production line zinc oxide desulfurization gypsum kaolin chromium)
REQUEST A QUOTE
RELATED PRODUCTS
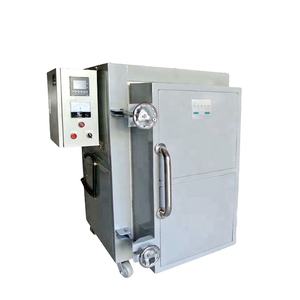
Large Gear For rotary kiln Casting Steel rotary kiln parts Ball Mill Gears For
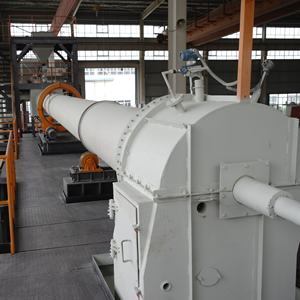
Factory Dri Direct Reduced Iron Rotary Kiln Plant Zinc Oxide Rotary Kiln for Sponge Iron
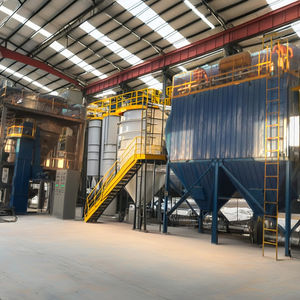
OEM Cement Factory Forging Rotary Kiln Support Wheel Trunnion Roller
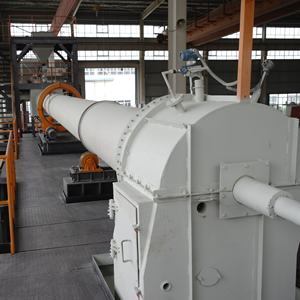
Best ing Limestone Rotary Kiln / Calcining Kiln Rotary Kiln / Clay Calcination Rotary Kiln for Magnesite and Hematite
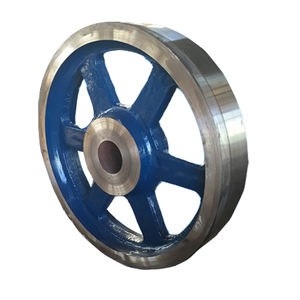
Clay Aggregate Production Line Ceramic Pelletizer LECA Rotary Kiln Factory Direct
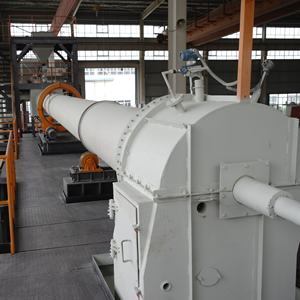