PRODUCT PARAMETERS
Description
Introduction of Industrial Calcination Rotary Kiln For Kaolin
A rotary kiln is a kind of industrial equipment used for material heating and processing, which is widely used in cement, metallurgy, chemical industry, etc. Industrial Calcination Rotary Kiln For Kaolin refers to various parts and components which are necessary for maintaining and repairing the normal operation of the rotary kiln, such as cylinder, baffle wheel, pallet, sealing device and so on.
Features and advantages of Industrial Calcination Rotary Kiln For Kaolin
High-temperature resistance: Due to the extremely high temperature of the working environment of the rotary kiln, the spare parts are usually made of refractory materials or special alloys to ensure that they can work stably under high temperatures.
High abrasion resistance: Long time material friction and chemical erosion require spare parts to have excellent abrasion resistance to prolong service life.
High structural strength: in order to withstand heavy loads and the pressure of continuous operation, the design of spare parts will place special emphasis on structural strength and reliability.
Easy to install and maintain: Considering the need for frequent replacement, many spare parts are designed to be simpler and easier for quick installation and maintenance.
Strong adaptability: different industries have different needs for rotary kilns, so spare parts need to have good versatility and adaptability to meet diverse application conditions.
(Industrial Calcination Rotary Kiln For Kaolin)
Specifications of Industrial Calcination Rotary Kiln For Kaolin
This commercial calcination rotary kiln procedures kaolin powder effectively. It transforms raw kaolin right into high-grade calcined kaolin for numerous industries. The kiln operates dependably under requiring problems.
The kiln reaches high temperatures needed for kaolin calcination. Temperature levels generally vary from 800 ° C to 1100 ° C. Exact temperature level control makes sure constant item high quality. Consistent heating takes place throughout the product bed.
Challenging products develop the kiln shell. State-of-the-art steel offers strength for constant operation. Refractory blocks line the within. This lining withstands extreme heat and shields the covering. The kiln turns gradually on durable support rollers. Durable drive systems make sure smooth turning.
The kiln tube is large. Usual sizes are between 2.5 meters and 4.5 meters. Lengths commonly range from 40 meters to 80 meters. Dimension depends upon needed production volume. Bigger kilns take care of even more material per hour.
Processing ability differs considerably. Smaller sized kilns manage 5 lots per day. Large installments can surpass 500 heaps daily. The kiln layout enhances warm transfer. This boosts effectiveness and reduces fuel costs.
Indirect or direct shooting warms the kiln. Typical gas are natural gas, coal powder, or diesel. Advanced heater systems guarantee full combustion. Warm recuperation systems capture waste gases. This preheats inbound burning air.
The kiln layout reduces warmth loss. Great insulation maintains energy consumption down. This saves money and reduces environmental influence. The kiln operates constantly for extended periods. Low upkeep is a vital attribute. Durable components reduce downtime. The kiln takes care of abrasive kaolin powder dependably. It does the job well in harsh industrial setups.
(Industrial Calcination Rotary Kiln For Kaolin)
Applications of Industrial Calcination Rotary Kiln For Kaolin
Industrial calcination rotary kilns are vital for refining kaolin clay. These large, revolving cylinders warmth kaolin to really heats. This intense warm changes the kaolin’s framework. The process burns off impurities and drives off water chemically bound within the clay. This causes calcined kaolin, a material with premium residential properties contrasted to raw kaolin.
The paper industry greatly relies upon calcined kaolin. It functions as a costs coating and filler pigment. Calcined kaolin boosts paper’s illumination considerably. It likewise enhances paper’s opacity and printability. This makes published text and images sharper on the page.
Calcined kaolin is important in paints and finishes. Its illumination and opacity help produce whiter, a lot more concealing paints. It enhances the paint’s durability and resistance to weathering. Repaint makers worth its constant performance.
Ceramics benefit greatly from calcined kaolin. Adding it to ceramic bodies enhances their stamina. It likewise enhances the whiteness of the final fired item. This is crucial for top quality floor tiles, sanitaryware, and tableware. Calcined kaolin likewise aids regulate the firing shrinking of porcelains.
The rubber market makes use of calcined kaolin as a useful filler. It enhances rubber compounds. This improves the toughness and abrasion resistance of rubber items like tires and hoses. Its brightness is an advantage in some tinted rubber items. Calcined kaolin also enhances electric insulation residential properties in rubber cables and wires.
Plastics manufacturers include calcined kaolin also. It works as a filler and extender. It boosts the rigidity and dimensional security of plastic components. Its illumination adds to the look of white and light plastic things. Calcined kaolin assists plastics withstand chemical destruction.
These kilns supply accurate temperature level control. This control is vital to achieving the precise homes needed for each application. The rotation ensures the kaolin heats equally throughout the procedure. Consistent item quality is a significant end result. Industrial calcination rotating kilns are the proven technique for generating high-performance calcined kaolin throughout several sectors.
Company Introduction
Established in 2001, plant Machinery Equipment Co.,ltd. focus on metal research and mining machinery spare parts. 2 factories over an area of 13,300 square meters, based on 100+ sets of equipment, our production capacity reaches 12000 Tons/Year. has passed ISO 9001 quality managment system certification in 2008.
Our mainly products are dragline excavator spare parts,rotary kiln spare parts, large modulus gear (gear shaft), gearbox ect. 40+ patents with over 45 years experience to help focus on improve the service life of spare parts. We belive that more than 80% reason of mechanical parts’ working life depends on hot processing (steel making/forging/casting/welding/heat treatment). Eight material engineers will control the quality from the original resource.
If you are interested, please feel free to contact us.
Payment
L/C, T/T, Western Union, Paypal, Credit Card etc.
Shipment
By sea, by air, by express, as customers request.
5 FAQs of Industrial Calcination Rotary Kiln For Kaolin
What does this industrial calcination rotary kiln do?
It heats kaolin clay powder very hot. This process is calcination. The heat changes the kaolin’s structure. It removes water and organic impurities. The result is metakaolin or calcined kaolin. This material has better brightness, whiteness, and hardness. Industries use it in paper, ceramics, paints, and plastics.
Why use a rotary kiln for kaolin calcination?
Rotary kilns work very well for powders like kaolin. The long, rotating cylinder tumbles the material. This ensures even heating. The tumbling exposes all particles to the heat. The kiln provides precise temperature control. This control is vital for consistent product quality. The design handles large volumes efficiently.
What factors affect the final kaolin quality?
The kiln temperature is critical. Too low, impurities remain. Too high, the kaolin sinters or degrades. The heating time inside the kiln matters. The rotation speed controls the material’s movement. The feed rate must be steady. The fuel type and air flow influence the atmosphere. Consistent control of these factors ensures the best metakaolin.
Is this kiln energy efficient?
Yes, modern designs focus on saving energy. Good insulation minimizes heat loss. Advanced burners achieve complete fuel combustion. Heat recovery systems are often used. Hot exhaust gases preheat incoming air. This reuse cuts fuel costs significantly. Efficient operation lowers production expenses.
How much maintenance does the kiln need?
Rotary kilns are robust but need regular checks. Refractory linings wear over time. They require inspection and periodic replacement. Mechanical components like rollers and drive gears need lubrication. Bearings and seals need monitoring. Planned maintenance prevents unexpected downtime. Proper upkeep ensures long service life.
(Industrial Calcination Rotary Kiln For Kaolin)
REQUEST A QUOTE
RELATED PRODUCTS
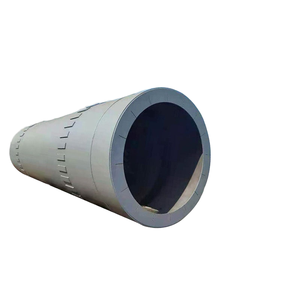
220v 380v Industrial Electric Screw Barrel Band Heater Element Ceramic Coil For Plastic Mould Machine
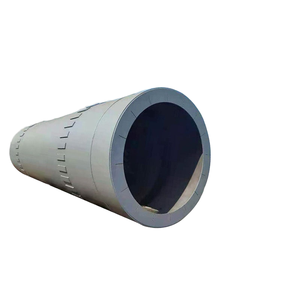
Chinese / OEM/ Spare Parts/ Support Roller for Rotary Kiln/ Made to order
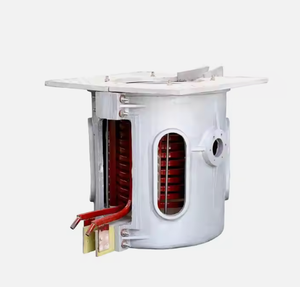
High quality Cement plant rotary kiln replacement parts large module ring gear
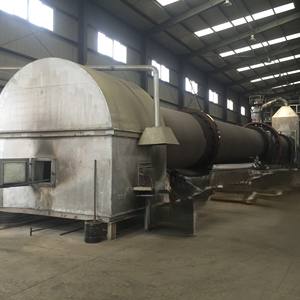
bauxite periodic rotary kiln cement 1000c cement kiln cooling fan and spare parts rotary valve for kiln machine
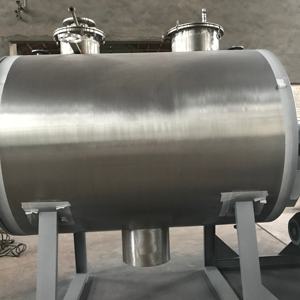
Cast Iron Steel Rotary Kiln Spare Parts Roller rotary Kiln Tyre rotary kiln wheel belt for cement and mining machinery
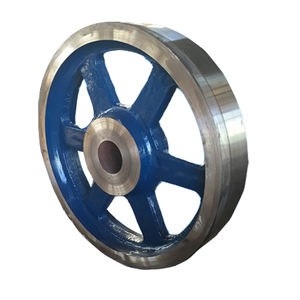