PRODUCT PARAMETERS
Description
Introduction of Rotary Kiln/ Zinc Oxide Production Line Rotary Kiln
A rotary kiln is a kind of industrial equipment used for material heating and processing, which is widely used in cement, metallurgy, chemical industry, etc. Rotary Kiln/ Zinc Oxide Production Line Rotary Kiln refers to various parts and components which are necessary for maintaining and repairing the normal operation of the rotary kiln, such as cylinder, baffle wheel, pallet, sealing device and so on.
Features and advantages of Rotary Kiln/ Zinc Oxide Production Line Rotary Kiln
High-temperature resistance: Due to the extremely high temperature of the working environment of the rotary kiln, the spare parts are usually made of refractory materials or special alloys to ensure that they can work stably under high temperatures.
High abrasion resistance: Long time material friction and chemical erosion require spare parts to have excellent abrasion resistance to prolong service life.
High structural strength: in order to withstand heavy loads and the pressure of continuous operation, the design of spare parts will place special emphasis on structural strength and reliability.
Easy to install and maintain: Considering the need for frequent replacement, many spare parts are designed to be simpler and easier for quick installation and maintenance.
Strong adaptability: different industries have different needs for rotary kilns, so spare parts need to have good versatility and adaptability to meet diverse application conditions.
(Rotary Kiln/ Zinc Oxide Production Line Rotary Kiln)
Specifications of Rotary Kiln/ Zinc Oxide Production Line Rotary Kiln
This rotating kiln takes care of zinc oxide manufacturing. It refines zinc concentrates into high-purity zinc oxide. The kiln body is long and round. It’s made from thick steel plates. Refractory bricks line the inside. This lining withstands extreme warm. It protects the steel shell.
The kiln rotates gradually. Its rate is adjustable. Operators control this thoroughly. Rotation blends the product. It guarantees even heating. The kiln tilts somewhat downhill. This helps material step through. Feed enters the top end. Ended up product exits the lower end.
Warm is crucial. Burners fire directly into the kiln. They make use of fuel oil or gas. Temperatures reach extremely high levels. Accurate temperature control is essential. Different areas need different warms. This drives the chemical reactions. It evaporates zinc. It calcines the product.
Air movement is taken care of proactively. Fans supply combustion air. Exhaust gases exit the kiln. They go through pollution controls. This catches dust and fumes. It satisfies ecological criteria.
The kiln sits on assistance rollers. Huge equipment rings drive the turning. Effective electric motors provide the force. Thrust rollers keep it aligned. They stop axial movement. This arrangement is durable. It takes care of heavy loads reliably.
Product feed is continuous. A controlled feeder supplies focus. Discharge is likewise continual. Item goes to cooling down systems. Then it mosts likely to packaging. Automation monitors vital criteria. Operators watch temperature, speed, stress. This ensures stable procedure. It keeps item quality.
(Rotary Kiln/ Zinc Oxide Production Line Rotary Kiln)
Applications of Rotary Kiln/ Zinc Oxide Production Line Rotary Kiln
Rotating kilns are vital devices in several markets. These long, turning cylinders manage high-temperature processes dependably. One key application is zinc oxide manufacturing. This material is essential for rubber, porcelains, pharmaceuticals, and more. Making zinc oxide requires certain problems. Rotary kilns offer these perfectly.
The zinc oxide manufacturing process starts with zinc-containing products. Usually this is zinc ore concentrate or zinc ash recycled from other procedures. Workers feed this raw material into the greater end of the somewhat inclined rotating kiln. The kiln revolves slowly. This turning relocates the material slowly down towards the hotter, reduced end. Fuel heaters fire directly into this lower section. Temperatures here get to over 1000 ° C, occasionally a lot greater.
This extreme warm drives off pollutants. It causes important chain reaction. Most importantly, it transforms zinc substances into zinc vapor. The vapor takes a trip back up the kiln versus the product circulation. Air enters the kiln’s upper end. This air cools down the zinc vapor. The vapor oxidizes. It turns into great zinc oxide powder. The powder exits the kiln with the exhaust gases. Cyclones and bag filters record the beneficial zinc oxide item. The staying waste material, called clinker, discharges from the kiln’s lower end.
Rotating kilns use substantial benefits for zinc oxide. They deal with continual handling of big volumes. Their style ensures outstanding warmth transfer performance. The product gets extensively blended and exposed to warmth. Operators locate rotating kilns durable and reasonably straightforward to preserve. Their versatility permits making use of various zinc feedstocks. This rotary kiln procedure, referred to as calcination, is verified. It provides consistent, high-purity zinc oxide for requiring applications. The kiln’s resilience converts to dependable procedure.
Company Introduction
Established in 2001, plant Machinery Equipment Co.,ltd. focus on metal research and mining machinery spare parts. 2 factories over an area of 13,300 square meters, based on 100+ sets of equipment, our production capacity reaches 12000 Tons/Year. has passed ISO 9001 quality managment system certification in 2008.
Our mainly products are dragline excavator spare parts,rotary kiln spare parts, large modulus gear (gear shaft), gearbox ect. 40+ patents with over 45 years experience to help focus on improve the service life of spare parts. We belive that more than 80% reason of mechanical parts’ working life depends on hot processing (steel making/forging/casting/welding/heat treatment). Eight material engineers will control the quality from the original resource.
If you are interested, please feel free to contact us.
Payment
L/C, T/T, Western Union, Paypal, Credit Card etc.
Shipment
By sea, by air, by express, as customers request.
5 FAQs of Rotary Kiln/ Zinc Oxide Production Line Rotary Kiln
What is a rotary kiln for zinc oxide production? It’s a long, rotating furnace. It processes zinc materials into zinc oxide. The kiln uses high heat. This heat causes chemical reactions. These reactions turn raw materials into zinc oxide powder.
How does the rotary kiln create zinc oxide? Zinc ore or waste enters one end. The kiln rotates slowly. The material moves toward the hotter end. Burners heat the material inside. Zinc evaporates. Then it reacts with oxygen. This forms zinc oxide vapor. The vapor cools. It becomes solid zinc oxide powder.
What are the main parts of a rotary kiln? The shell is steel. Refractory bricks line the inside. They protect the shell from heat. Support rollers hold the kiln. They let it rotate. A drive system turns the kiln. Seals stop air leaks. A dust collection system catches zinc oxide powder.
Why use a rotary kiln for zinc oxide? It handles many materials. It works with low-grade ores. It handles zinc waste too. The process is continuous. It saves energy. It produces pure zinc oxide. The powder is fine. It works for industries like rubber or ceramics.
How do you maintain a rotary kiln? Check the refractory lining often. Fix cracks quickly. Monitor the bearings. Lubricate them regularly. Watch the seals. Replace them if damaged. Clean the dust system daily. Balance the kiln rotation. This stops uneven wear. Schedule shutdowns for big inspections.
(Rotary Kiln/ Zinc Oxide Production Line Rotary Kiln)
REQUEST A QUOTE
RELATED PRODUCTS
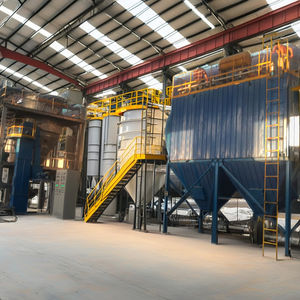
Factory Customized Rotary Kiln Parts Cement Plant Forged Large Gear Ring
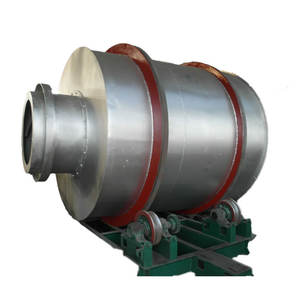
Citic Rotary kiln spare parts Rotary kiln supporting wheel bearing device Rotary kiln
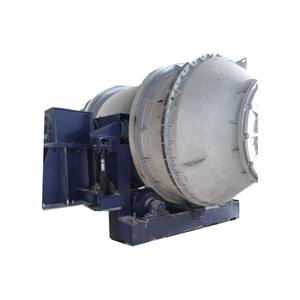
rotary-kiln-burner rotary drying kiln rotary kiln seal
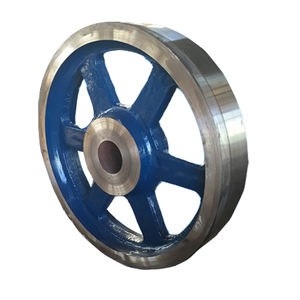
China New Product Rotary Kiln Burner For Cement
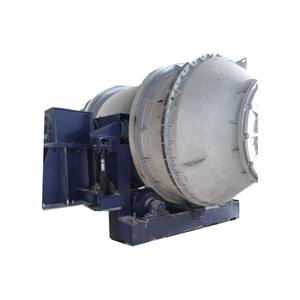
Haishan Brass Bush Heavy Machinery Spare Parts Precision Bronze Bushings
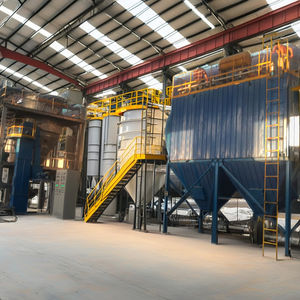